Plastic Film Granulation Line
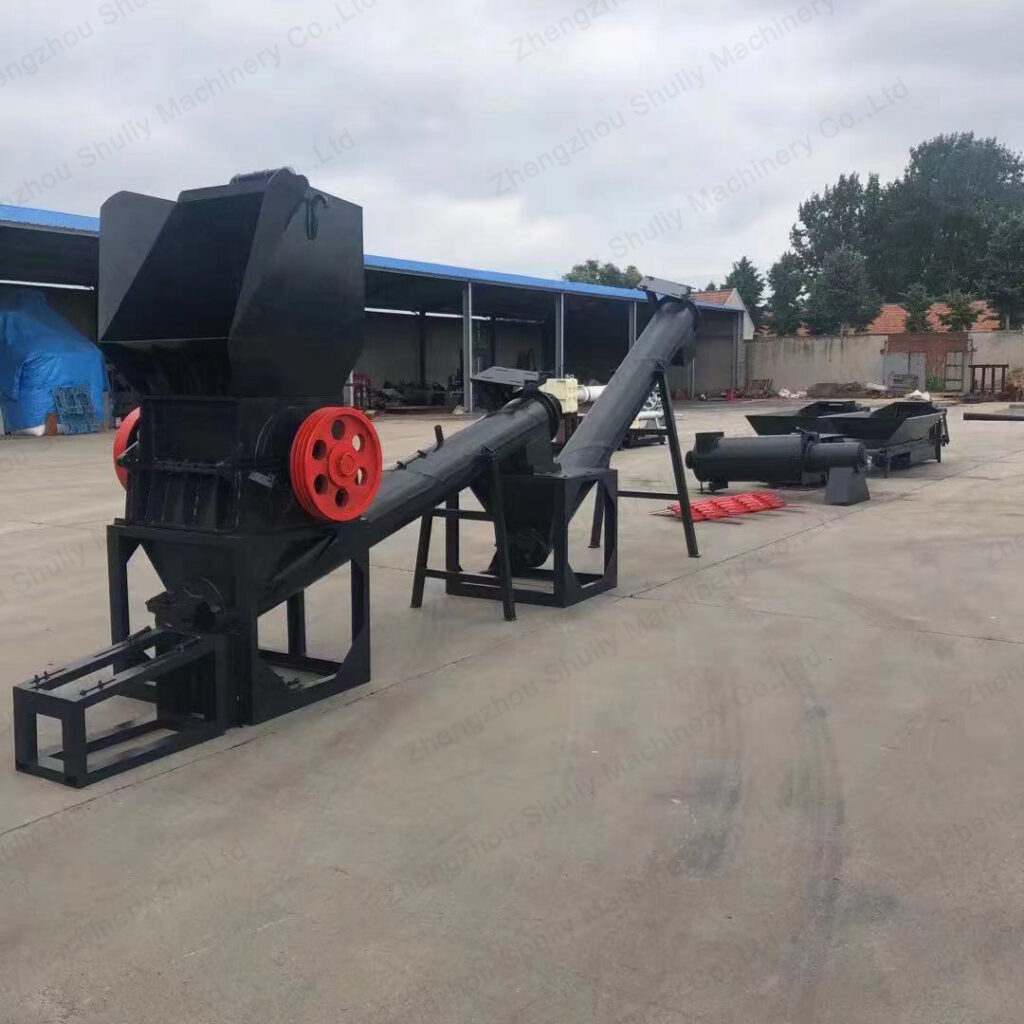
Plastic film Granulation Line are mainly used to recycle PP, PE films, woven bags, shopping bags, waste packaging plastics, agricultural films, etc. This article mainly introduces the process flow, application, characteristics, main equipment, etc. The capacity of our Plastic Film Granulation Line ranges from 200 kg/h to 2000 kg/h. While our standard rigid PE plastic flake pelletizing lines are sufficient to meet the needs of most facilities, custom settings with additional mechanical configurations and increased throughput can be designed to meet your specific needs. Please contact us for more information on custom recycling projects!
Video of granulation line operation
Shuliy Machinery is a professional supplier of plastic film granulation line, experienced in production, and can be customized according to your needs, welcome to contact us.
Introduction of plastic film recycling line
PE PP film washing line specializes in recycling various waste films and woven bags. The entire PE granulation line consists of a plastic crusher, a plastic washing machine, a vertical lifting dehydrator, a plastic granulator, a cooling tank, a granulator and a storage tank. The waste plastic film recycling and granulation Line is a solution designed specifically for recycling waste PP PE LDPE HDPE films. The entire production line can produce non-stop and only requires 2-3 workers. The PE granulation line designed by Shuliy is popular in Mozambique, Nigeria, Ethiopia, Ghana and many other countries in the world. If you have similar plastic film recycling needs, please feel free to leave a message on the website.
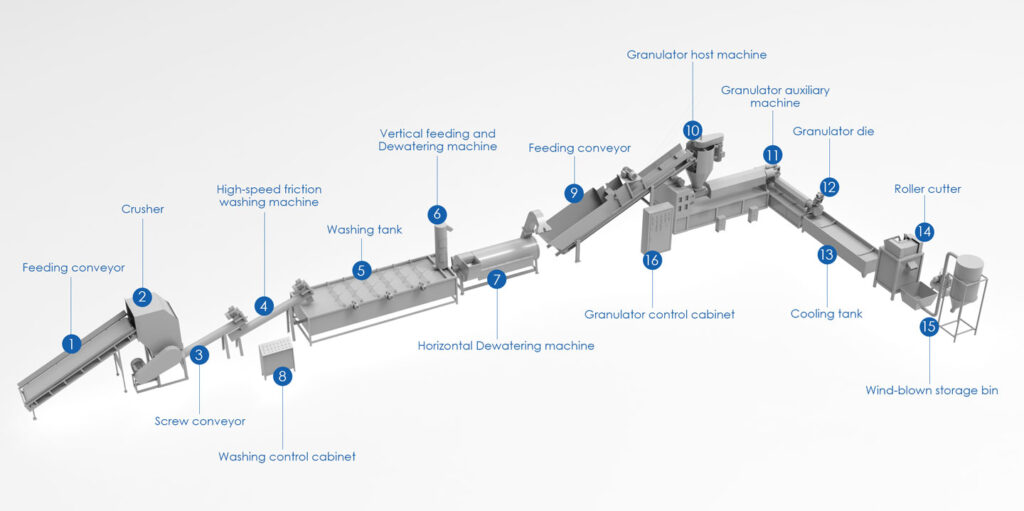
Process of Plastic Film Granulation Line
Crushing → Washing → Rinsing → Drying → Granulating → Drawing → Cutting → Packaging
First, for woven bags with large sand content, after cutting or shredding, make large rolls of woven film bags into small bundles of small piles, then screening and sand removal pretreatment, and then add water to wet crush into small fragments.
Second, the machine shredded film fragments through the special film woven bag high-speed friction machine strong scrubbing, removing most of the material surface sediment, and then rinse the material with water.
Finally, the rinsed and separated materials are sent into the squeezing and drying machine for dewatering. After washing and drying, the film-woven bags can enter the granulator for granulation.
Raw materials and finished products of plastic granulating line
Main machine of Plastic Film Granulation Line
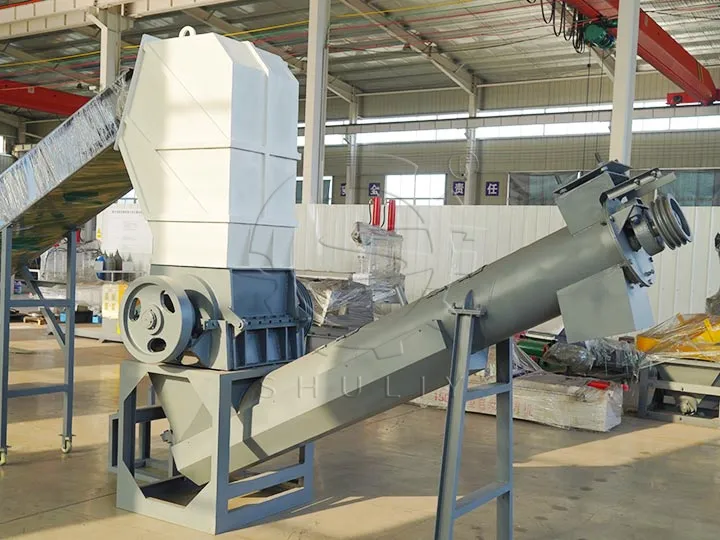
Step1 Crushing
Waste LFPE film is first fed into the first machine of the soft PVC granulation line, the plastic waste shredder machine. The plastic waste shredder machine is responsible for crushing large pieces of waste plastic film. This step is designed to reduce the size of the plastic, making it easier to pelletize.
Step2 Washing
The crushed plastic flakes enter the plastic washing machine. This machine washes the film pieces with water to remove impurities, dirt, and residue from them.
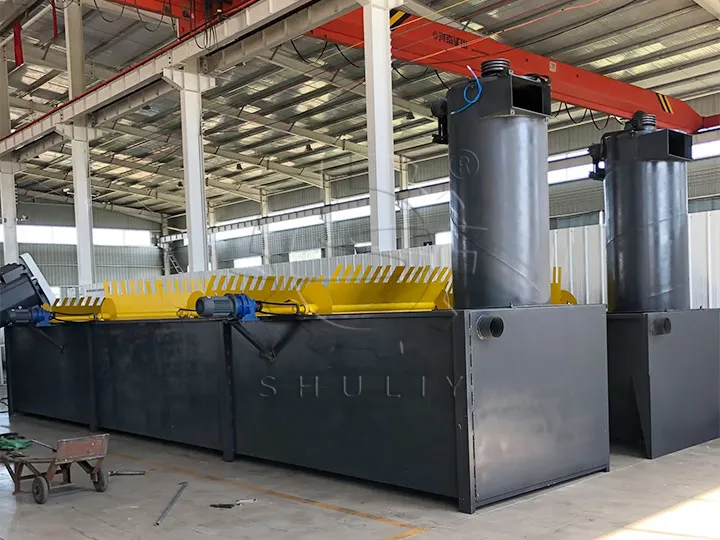
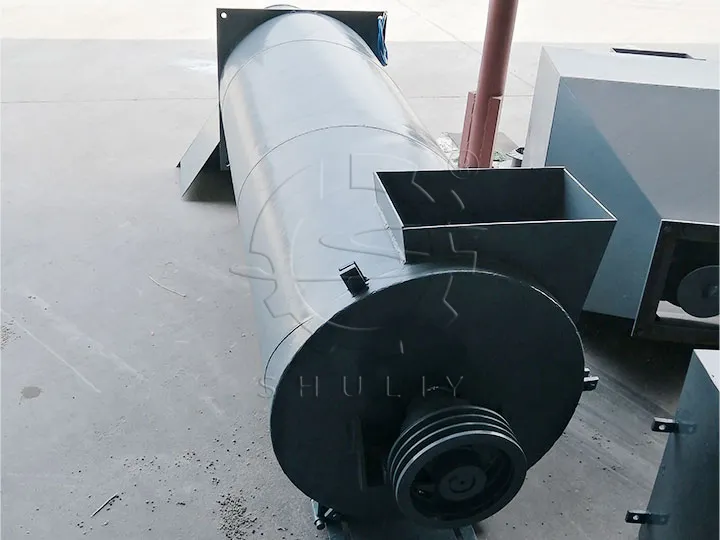
Step3 Drying
The cleaned plastic pieces are then passed through a vertical lifting dewatering machine, which removes moisture and ensures that the subsequent pelletizing process can be carried out efficiently.
NO.4 Granulation
The dried plastic fragments enter the plastic pelletizer machine, where they are compressed into small granular shapes by melting and extruding them to become reusable plastic pellets.
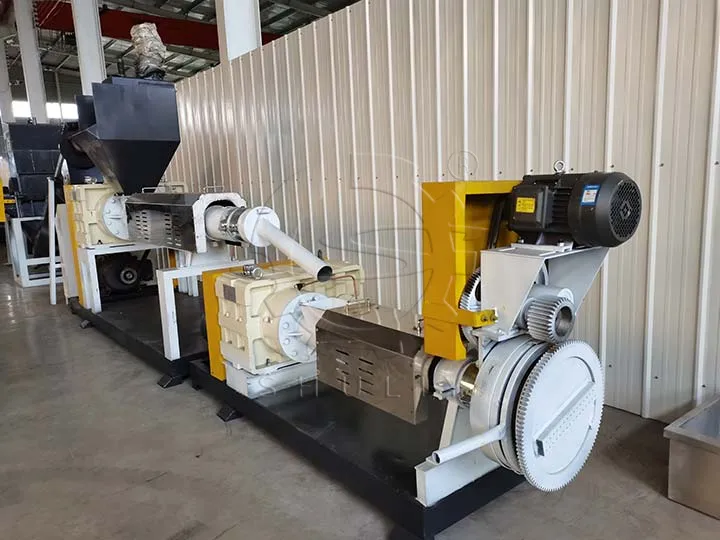
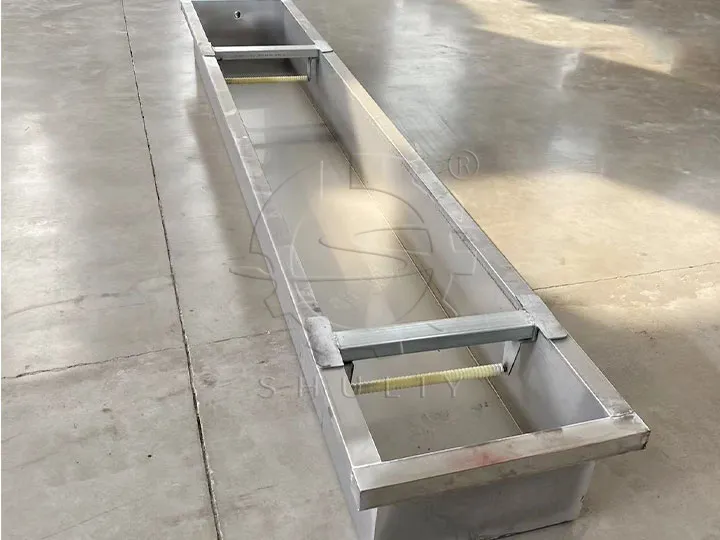
NO.5 Cooling
After pelletizing, plastic strips will soften due to high temperatures and will not be able to be cut with a pellet cutter machine. A cooling process is therefore required to ensure that they remain in a stable form.
NO.6 Cutting
The cooled plastic strips are cut into uniform plastic pellets. Finally, these plastic pellets are collected and packaged as needed for transportation and storage.
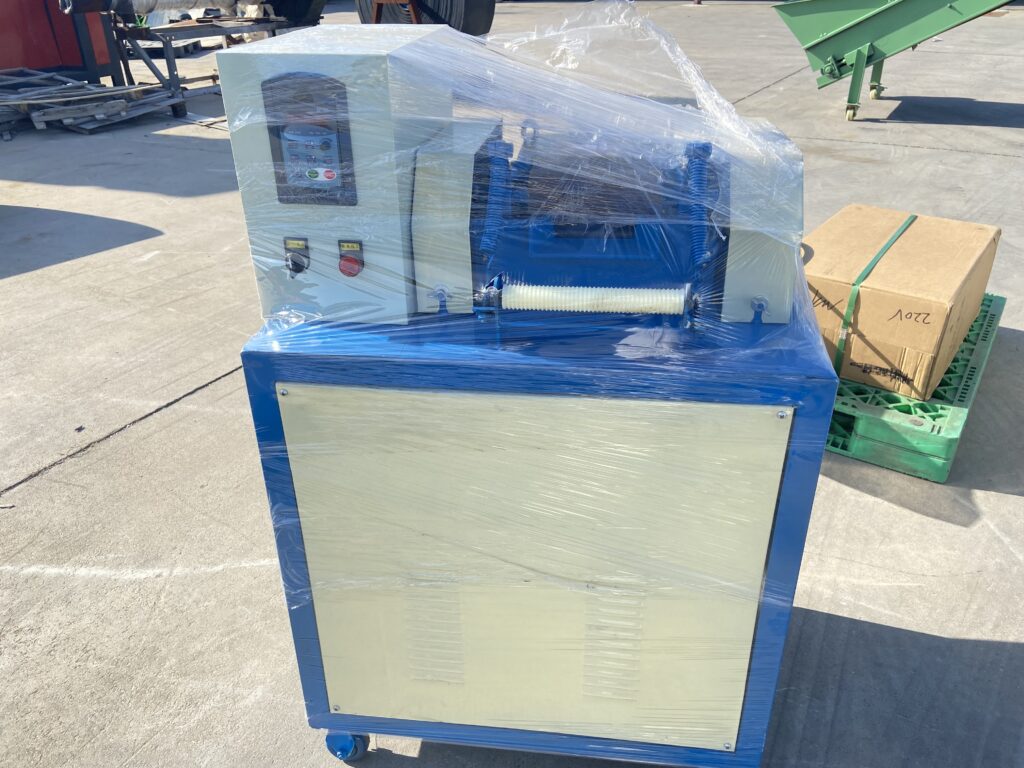
Features of plastic film Granulation Line
- The use of a circulating water system ensures the cleaning effect while controlling the water flow and evaporation of water
- Targeted design of the fine crushing system, the size of the crushed film is even and easy to clean
- The rinsing water tank adopts claw-type uniform discharge to ensure uniform discharge and control the water content at the same time, providing a process basis for the dewatering module
- The moisture content of the finished product is strictly controlled to 5%, which is suitable for high-quality granulation requirements.
- After theoretical calculations and repeated measurements, the mechanical operation details of the crushing, cleaning, and drying process are adjusted to avoid material loss due to excessive processing
- Automatic control of the whole LDPE film washing line, the system units are linked to operating, maximizing production capacity, and at the same time have a prediction function for possible abnormalities to ensure system safety
- According to the production, requirements can be equipped with the corresponding plastic pelletizing lines.